services with a smile
services
maintenance
Whether you intend to make reactive maintenance (run to failure) or preventive maintenance, we can deploy on site the right team to work your maintenance tasks out: with deep knowledge of mechanical architecture of packing line machines and plenty of years of experience in maintenance execution, IPES team knows the most common reliability parameters (MTBF and time to failure for instance) to optimise your preventive maintenance schedule and outcome.
On the other hand, in case of run to failure approach, detailed troubleshooting sessions & brainstorming will be carried out by our team together with your team, so that proper knowledge transfer is guaranteed and the same failure won’t happen again the near future.
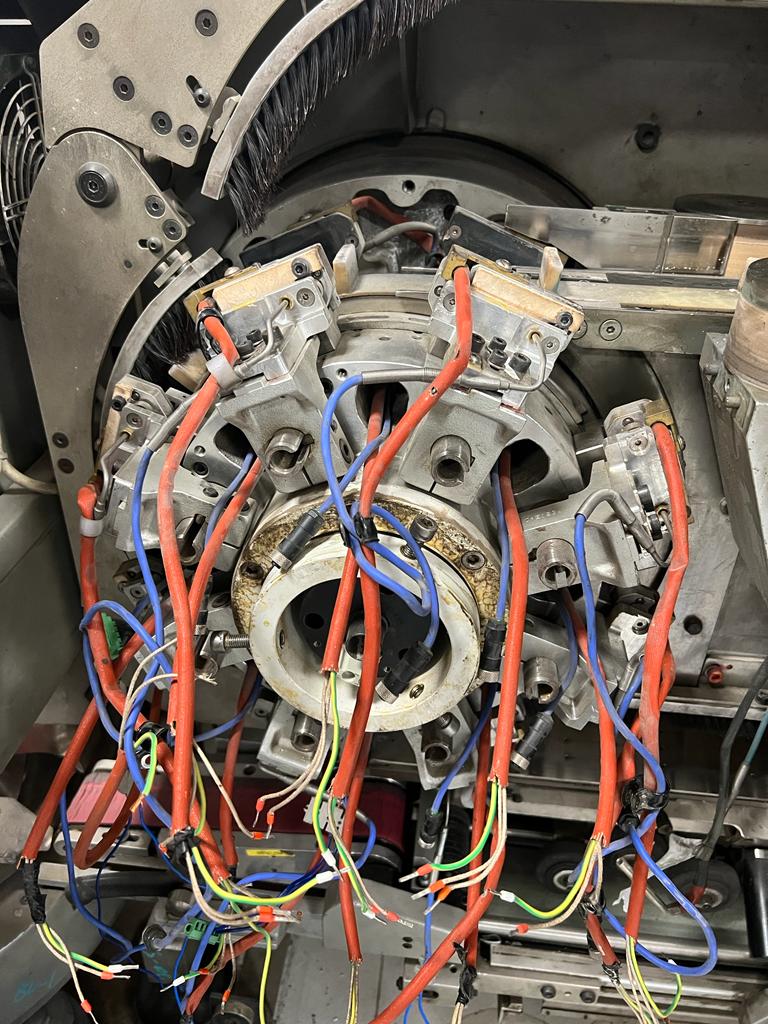
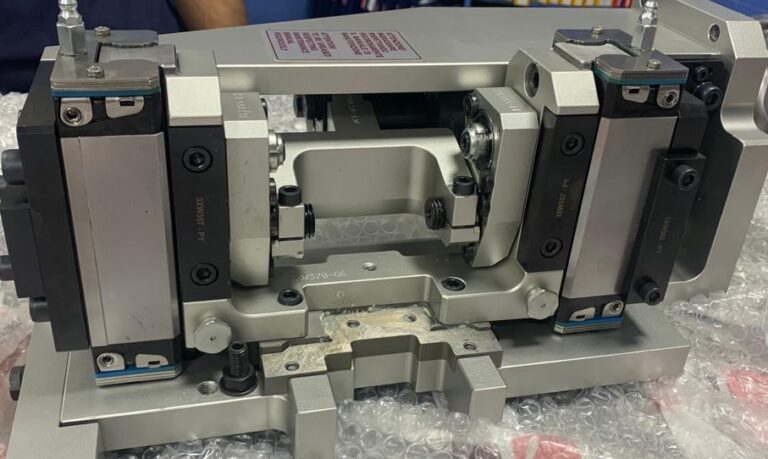
services
Installation Of Accessories & Upgrade Kits
Investments in accessories and/or upgrade kits is a good strategy to increase the performance or to catch up on with market requirements.
IPES teams are constantly updated to the latest technology level, when it comes to upgrade kits and accessories.
With a huge and spread experience in installation of accessories (like AN and CN stampers) and upgrade kits (like different versions of heating tunnel), IPES team is fully capable to support you in this kind of projects.
Once again, IPES approach is data driven, hence based on previous performance data, IPES guarantees the same level to reach after the intervention.
services
Format Change & Size Conversion Support
Whenever you are in need of technical support to install all required parts for format change (complete or partial) or for size conversion (cigarette dimensions change or whatsoever), we can deploy to customer’s premise the skilled team, to support you in the more accurate way on both mechanical side and electrical side.
No waste of time, just stick to planned time for intervention and performance back to the same level as before intervention are the goals we set for this kind of support.
Preliminary assessment of the involved line (3 to 4 days) is strongly recommended to optimise the entire project.
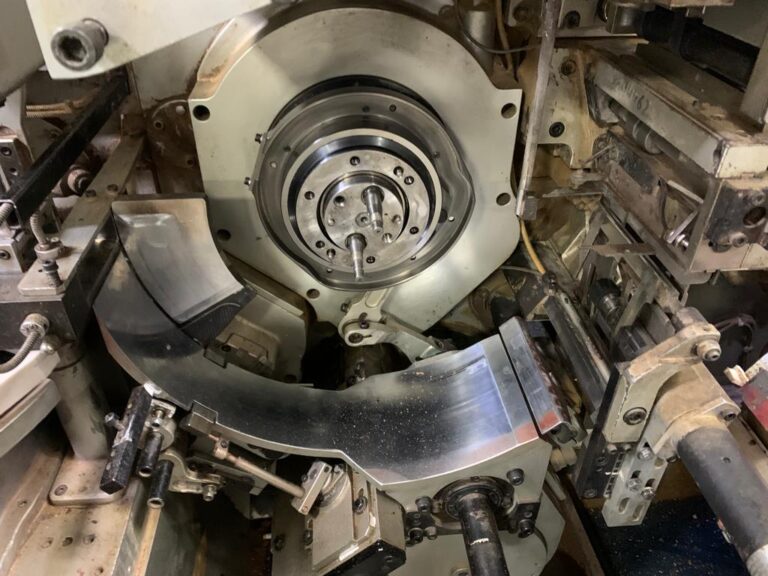
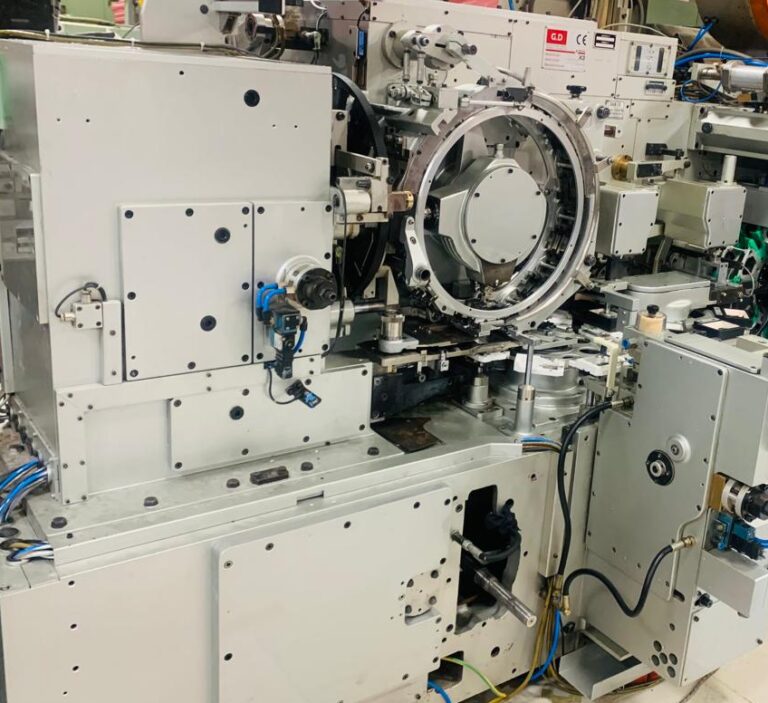
services
machines relocation
In a global world where business & market requirements change frequently and significantly, machines relocations happen more and more often:
This kind of activity is not an easy project to carry out.
IPES teams are capable to support you in each and every phase of the whole project: assessment of the machines in the original premise, editing the list of maintenance parts (mechanical and electrical) to install on the machines, helping with the disconnection and boxing of the machines in the original premise. Once the machines arrive in the final location, IPES team can support to unbox and connect the machines, install whatsoever upgrade kit or accessory purchased, install all the maintenance parts, run up of the entire line and stabilise the performance at the required level, up to the commissioning of the entire line.
services
Overhauling On Site
As soon as the machines reach a certain and significant amount of running hours (20.000 or more), a deep maintenance is required and the overhauling on site can represent a good technical option to increase the lifetime of the machines and bring the performance back to satisfactory level.
IPES teams, guided by technical supervisors, support customers in overhauling on site projects, working closely together: data collection of machines performance, technical assessment in order to prepare the list of spare parts required, preparing the more accurate working space/area are the preliminary activities IPES team will carry out.
Once the spare parts are available, IPES team will be dismantling the machines, install the spare parts, assemble again the machines, run up and commissioning of the line, in order to bring the performance at expected level.
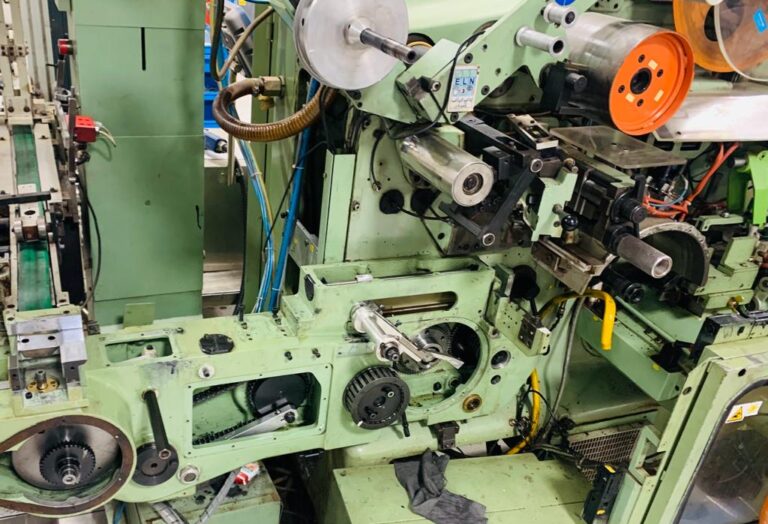
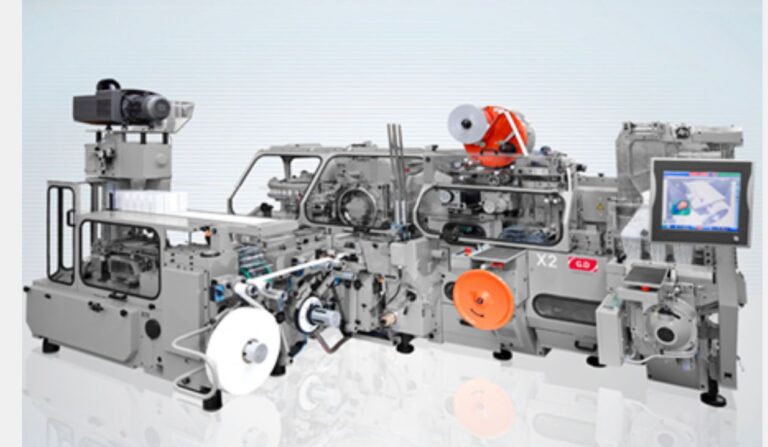
services
Performance Improvement Plan
IPES does know how important is getting even a small increase in performance, in terms of OEE or efficiency or stops reduction or rejects reduction.
IPES technical teams, coordinated by technical supervisors, are deployed on site to reach that goal: our team has a very data driven approach. In fact, IPES assesses the machines, analyses technical data provided and provides a list of tasks to accomplish to reach the goal.
All activities are carried out together with customer’s team, in order to share knowledge and fill the potential knowledge gap.
A tailored list of spare parts will be created, in order to improve the maintenance approach to the machines and keep the improved performance stable in the future.
services
training on site
Awareness of being in need of training represents the first step to increase the knowledge: IPES is right there to support our customers in the journey to get more knowledge.
In fact, with our experience over the years, we can tailor training solutions, based on customer technical areas of weakness: IPES fills the technical knowledge gap, both on mechanical and electrical field of experience.
Based on customer requirements, trainings can be developed on multiple steps, from theoretical sessions to “hands on” trials: learning by doing is IPES spirit to carry out trainings.
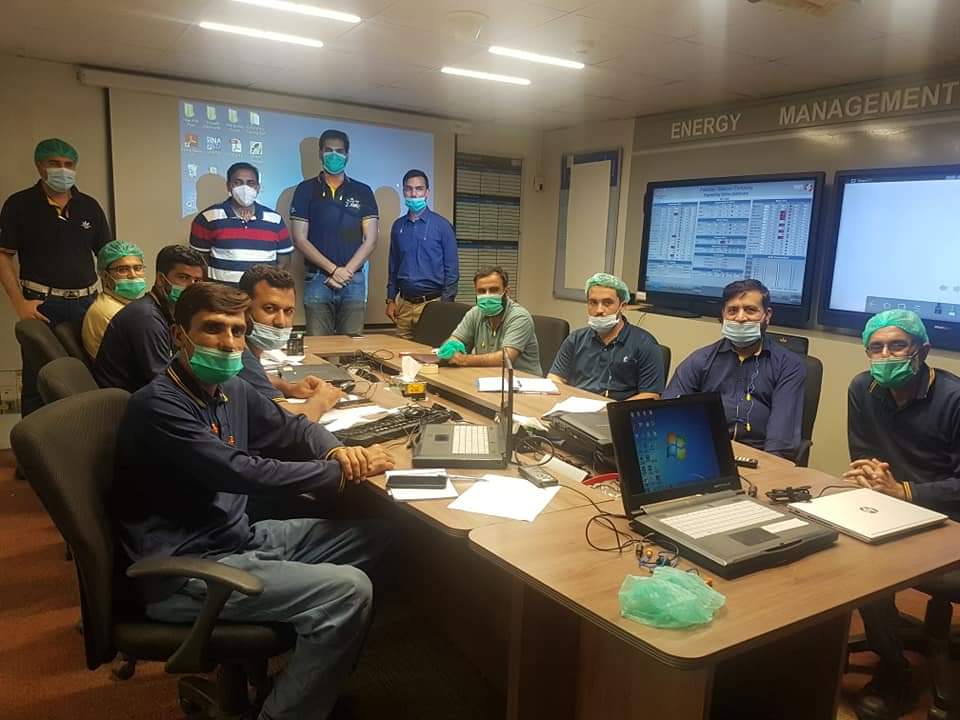
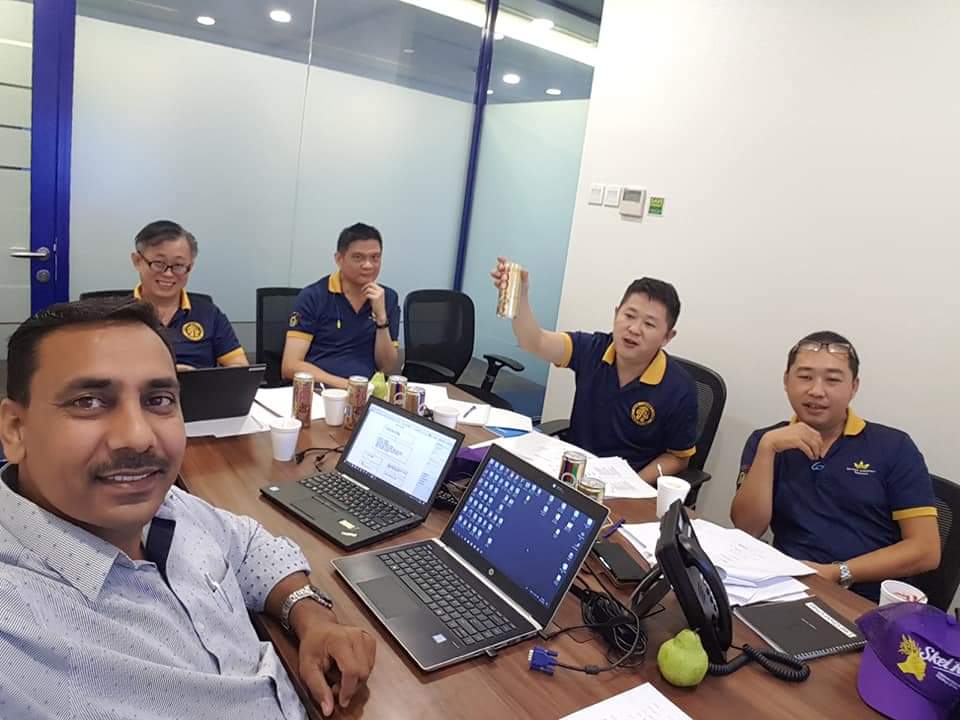
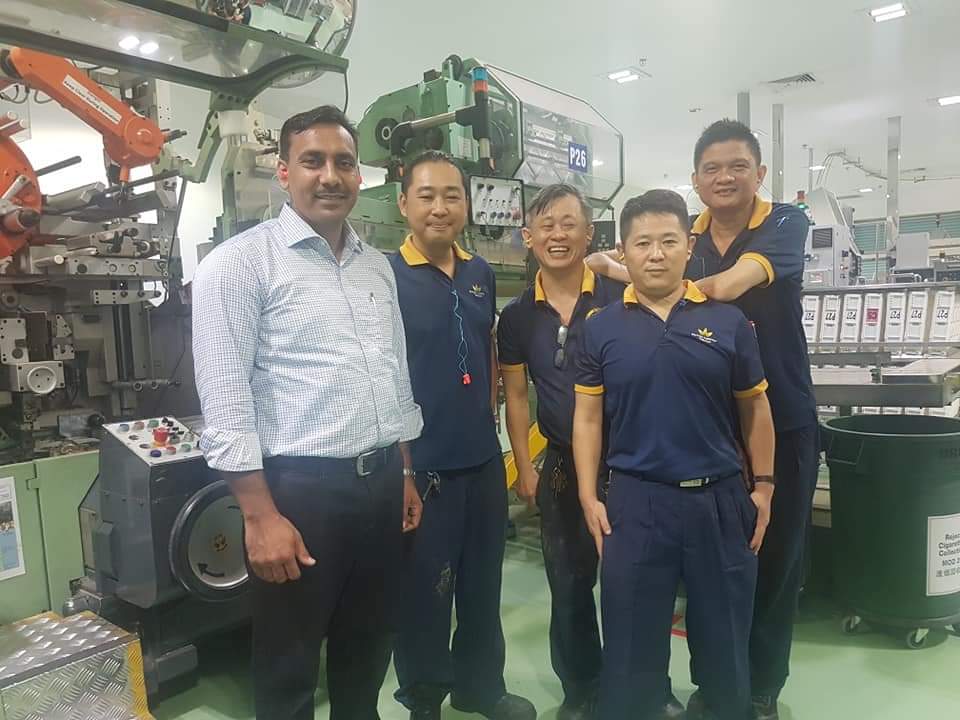
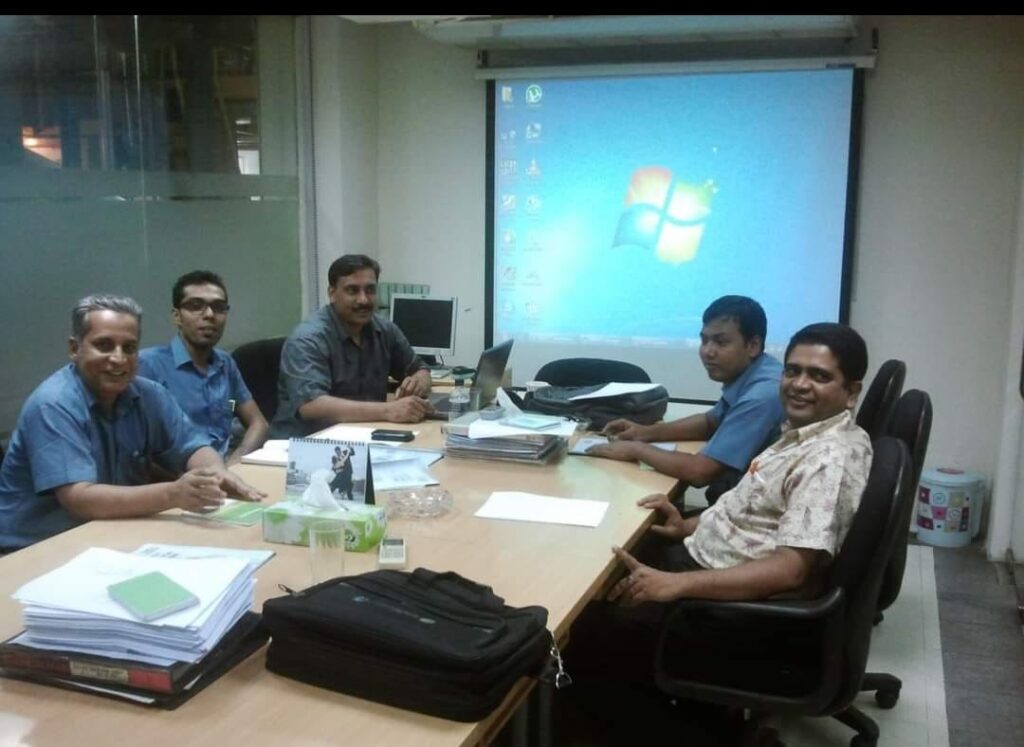
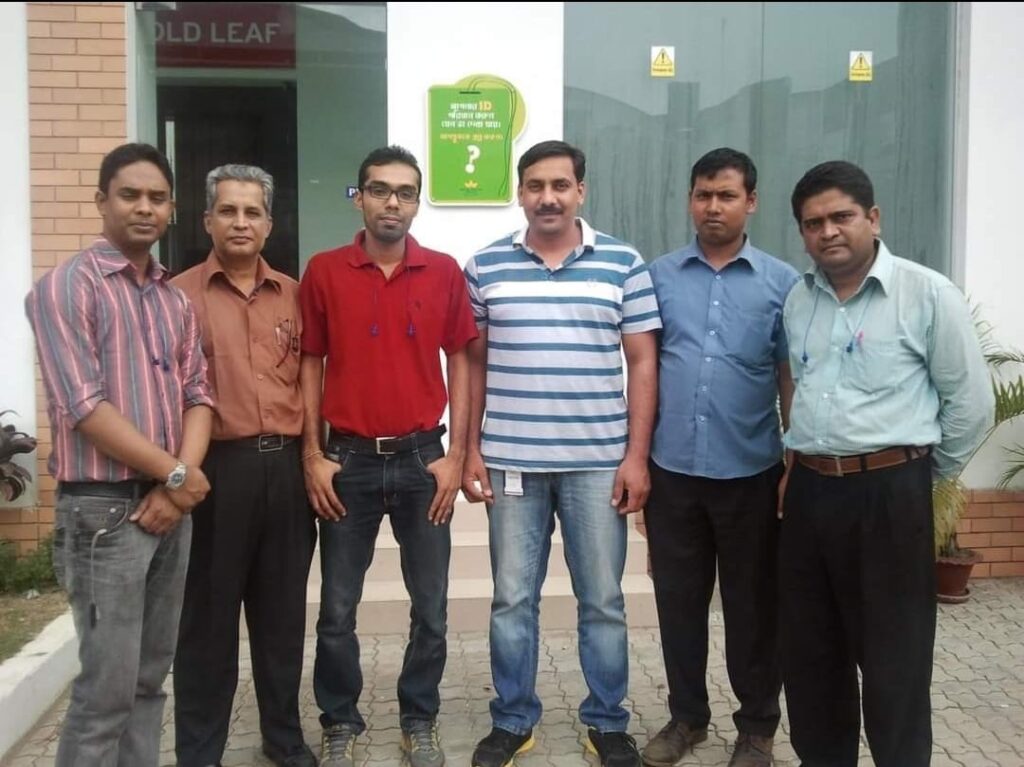